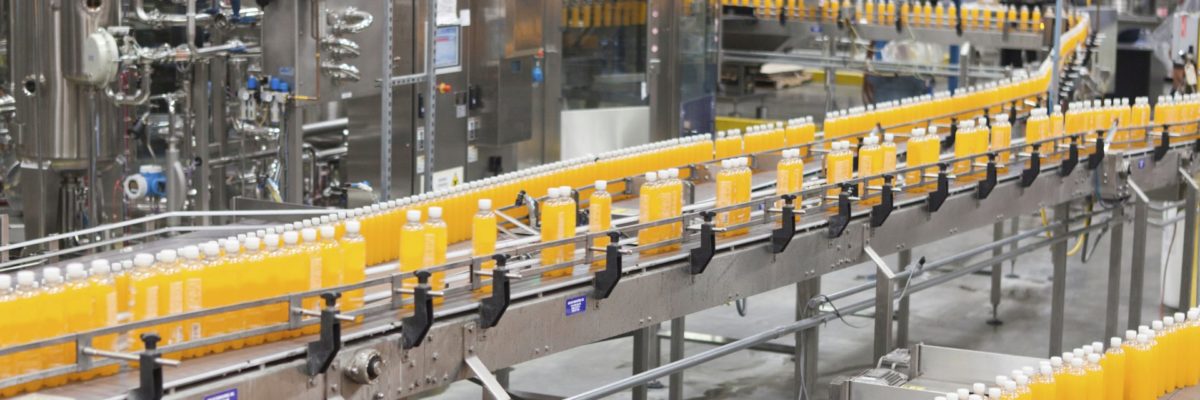
Markets
TCI provides a variety of solutions to improve power quality, reduce energy costs, extend motor life and performance, and protect sensitive equipment in food and beverage facilities. The company specializes in delivering the right product for the right application and offers the following solutions for any application:
Harmonic Distortion Solutions
High Frequency Noise Solutions
Motor Protection Solutions
In order for Food and Beverage plants to be profitable, they need continuous and high volume of production. Interruption to the production process can cause missed production volume which can be substantial. Lost productivity, idled workers, damaged in-process material, extra clean-up costs, restarting difficulties, delivery delays and-ultimately-upset customers can be the result.
Variable Frequency drives (VFDs) have become common in the food and beverage industry because they help achieve production volumes, energy savings, precision control and intelligent automation. However, VFDs create a large amount of the harmonic distortion in a food and beverage plants.
VFDs create harmonic distortion because the power loads are nonlinear and draw current with a waveform that doesn’t conform to the shape of the supply voltage. Harmonic distortion can increase electrical consumption and maintenance costs and cause wear and tear on motors and other equipment, power-quality problems and utility penalties for causing problems on the power grid.
Harmonic distortion can be produced in a plant and/or may enter a plant from the electric utility power system because of other sources on the line feeding the plant. IEEE 519 standards have tried to address this by defining responsibility for both the electric utility and the user. The major concern for the electric utility is the voltage quality while the industrial user is responsible for the level of current distortion.
Conveyor lines are effected by dV/dT due to reflective wave distortion, due to their long lead lengths. Motors are damaged by continued exposure to dV/dT.